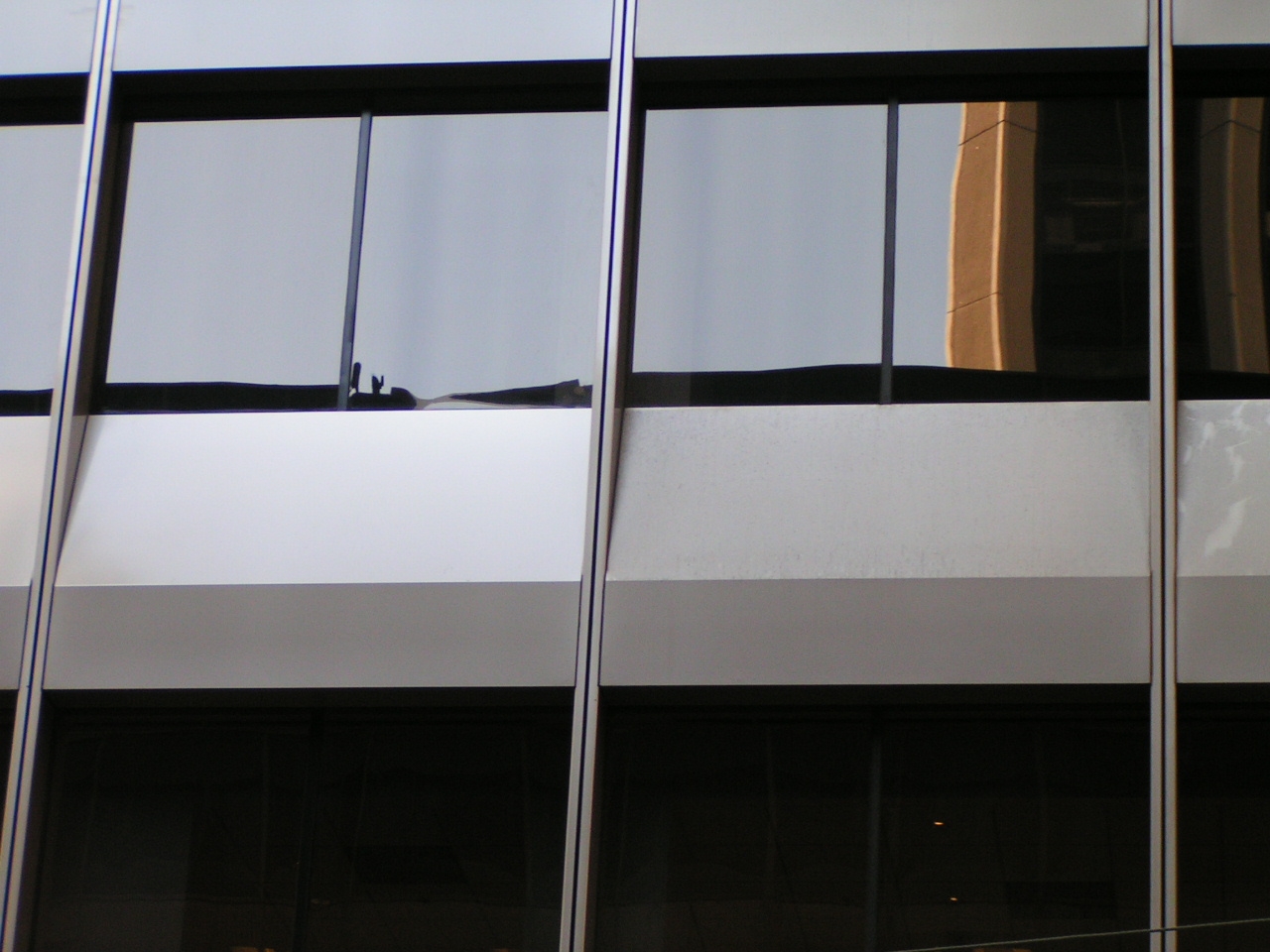
Anodized Aluminum Curtain Walls
This document is intended to assist those who manage office structures clad with anodized aluminum curtain wall systems (AACWS).
Specifically, its purpose to help them in decision making relative to planning and budgeting preventive maintenance (PM). The goal of this report is to raise awareness about the cost benefit of proactively caring for this critical and often overlooked major building system.
Why should one consider the condition of their aging anodized building façade?
- Protect Future Value and Effectively Manage Operating Costs – Generally, the cost to care for something and keep it for a long time is far less than to let it deteriorate to a point where major repair or replacement is required. A well-maintained building tends to command a higher value when marketed.
- Avoid Duplication of Cost – Planned PM can be bundled and scheduled with other similar One service provider may able to provide significant cost savings by a comprehensive approach that eliminates what would otherwise be redundant costs (such as rigging) and multiple contracts to administer.
- The “Curb Appeal” Factor: Image and Appearance Boost Prestige and Tenant Retention – Newer “Class A” surrounding buildings are presenting competition for attracting and retaining
When should one consider the condition of their aging anodized building façade?
- Plan, as Far Ahead as Possible – Metal and glass curtain wall clad structures, particularity those located in large cities where air quality is poor, will require certain and specific Eventually, a system failure will occur (i.e. leaks, window seals or weep systems fail, portions of the façade become detached). When this is the case, the repairs will become urgent. If repairs of this nature have not been factored into the building’s operating plans, cost control and effective- ness suffer. Using long term planning, management recognizes that time spent in planning saves time and expense in execution.
- Act before Deterioration is Abundantly Evident – Care for a building façade is akin to maintaining healthy teeth. Regular cleaning and inspection keeps you smiling, whereas a deferred visit to the dentist is sure to be painful and Deferred PM leads to restoration or replacement.
- Increased Frequency of PM Minimizes Complexity – Regular PM is generally very simple and rapidly executed. Restoration and replacement involves longer planning, testing, demolition and significant disruption to normal building
Maintenance Options
During the life of an AACWS, the options for the maintenance and restoration of such façades are limited. The chart below illustrates the three general options with a relationship to benefits and cost.
Typical factors that Drive AACWS Maintenance, Restoration or Replacement
- Architectural anodized aluminum declines in appearance and corrodes relative to:
- Initial design, system components/products and installation quality7
- Environmental exposure (natural elements, urban/industrial corrosive pollutants)8
- PM history, frequency and methods9
- Physical damage caused by window cleaning chemicals and equipment10
- Time in service
- The ability to maintain or restore the appearance of an AACWS, relative to its original condition, directly relates to the five factors identified
- The cost to maintain or restore the appearance of an AACWS, relative to its original condition, directly relates to the five factors identified
- The effects of deferred PM include:
- Irreparable damage the finish of the metal – (when you see it, it’s too late).
- Ever-increasing rate of corrosion following the breaching of the protective anodic layer (see Attachment on page 5).
- Loss of structural design
- The ingress of water through holes in the building façade caused by corrosion. This condition can necessitate the need to remove and replace portions of the building façade and lead to the need for major structural repairs.
- At a certain point, curtain wall system metal deterioration can only be corrected by the field application of high performance architectural finish systems, involving:
- A cost at least three to four times the cost of regular PM treatments
- Work schedule duration two to four times longer than regular PM
- Highly weather sensitive applications that make completion time uncertain
- Potential significant impact and disruption to the occupants of the building
- High-risk factors difficult to quantify related to public safety/environmental issues
As a service provider of the subject work, Stuart Dean provides information within its condition reports for clients to establish what can and cannot be achieved through the cleaning process. Here is how:
“The above detailed cleaning process is designed to improve the overall appearance and surface conditions of the façade without damaging the anodized finish. Cleaning and scrubbing cannot correct areas with conditions such as etched stains, as well as surface corrosion evidenced by pitting, particularly when advanced and widespread. These locations have suffered irreparable anodic finish damage. Existing surfaces deteriorated as such can only be cleaned and not more than lightly abraded. Further abrasive cleaning will expose more raw aluminum that has no natural corrosion resistance due to loss of the original anodic protective layer. The application of a clear curtain wall protectant is important as a corrosion inhibitor to surfaces compromised as mentioned above, as well as weathered yet undamaged surfaces, however existing corrosion damage will show through.”
For buildings that have received the benefit of regular PM, the above concerns do not apply.
- Typical time horizons based on Stuart Dean’s 70 years of metal maintenance/restoration experience
- The three examples shown reflect the primary façade treatment categories
- Regular effective PM suggested at five-year cycles, or more frequently
- Lack of PM drives Effective PM can defer restoration and replacement almost indefinitely
- Weather seals (caulking) have an average service life of 10-20 years (silicone sealant is 20 years plus)
- With little or no PM, significant façade component replacement is likely
- Initial building design and construction factors include: façade complexity, extent of horizontal surfaces that collect harmful contaminants, access limitations, and relative quality of specified system components and their installation.
- Typical rainfall, sun exposure, range of annual thermal cycle (min/max temps), buildings proximity to sources of acid rain and harmful airborne particulate matter
- Poorly executed cleaning methods and material may cause permanent damage
- The chemicals and equipment used in periodic window cleaning can seriously damage surrounding metal
Conclusion
Today, most building façades constructed with AACWS suffer from a lack of attention and scheduled cleaning. The reason is that corrosion problems related to air pollution and deferred maintenance are just now beginning to be understood. Unfortunately, many building managers and owners have operated under the belief that AACWS was virtually maintenance free. Many of these buildings are now reaching a critical point: The need to improve appearance and correct serious corrosion and water infiltration problems can no longer be postponed.
The good news is that with prompt action, many of these structures can have their façade appearance dramatically improved and their service life extended. To accomplish this, those responsible must find the right service provider who has the specialized knowledge and experience required. To save time and money, exercise care and choose a company that has a proven record of accomplishment, good references, and the information required to make wise decisions. This type of work is not well suited to inexperienced companies who simply submit the low bid. Many façades have suffered severe and permanent damage at the hands of those who thought, “this is just another cleaning job.”
Modern office towers constructed with anodized aluminum and glass, are very durable, yet they do require certain maintenance actions. These actions are inevitable if the cladding system is to remain attractive and provide the essential functions integral to their original design and safety. With good planning and prudent investment, these critical systems will continue to perform their vital role for many trouble-free years.
Summary
Stuart Dean Company has been helping to maintain and restore many of our nations’ most important buildings since 1932. The firm has the people and the information that building managers need to make wise and important decisions. Aware of how important façade services are to its clients, Stuart Dean has a team of industry specialists dedicated exclusively to this challenging field. The Special Services Group of the company consists of people with special skills and expertise related to building façades. They are devoted to responding to the complex and specific needs of each client’s façade enhancement and protection project. Stuart Dean Company has the people, experience, and desire to meet the requirements unique to each client.
Attachment
The following attachments contain charts and illustrations that further detail issues relative to the effective maintenance management of anodized aluminum building façades.
COMPARISON OF SURFACE STRUCTURE CHARACTERISTICS
New / well maintained versus poorly maintained architectural anodized aluminum.
Fig. 1. New/Well Maintained
Fig. 2. Poorly Maintained