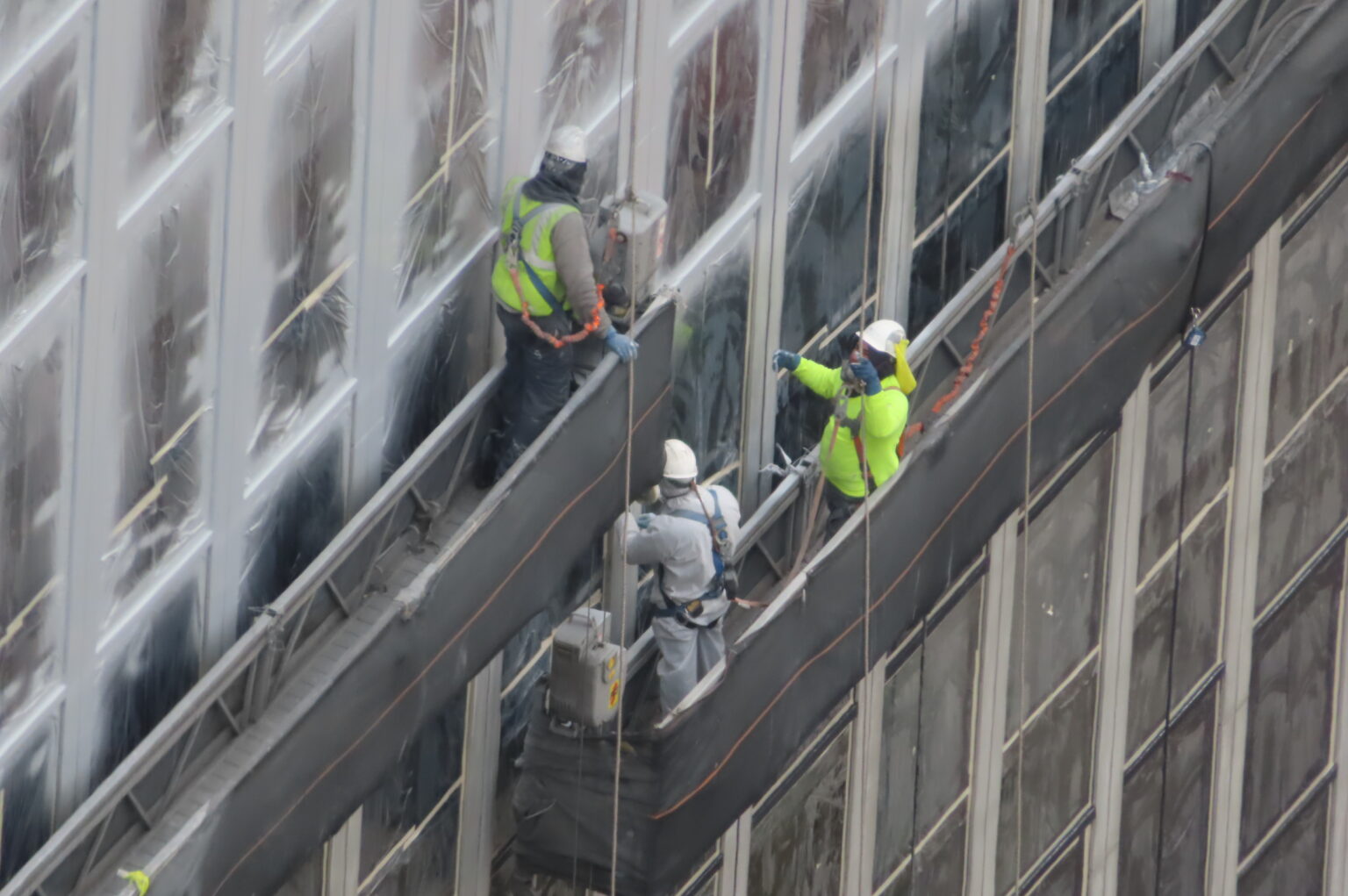
10100 Santa Monica Blvd.
Built in 1971, 10100 Santa Monica Blvd. is a 26-story office building in Century City, CA. The building (605,657 sq. ft.) is located adjacent to the Avenue of the Stars and is part of the gateway to Century City, one of the premier commercial submarkets in southern California.
Hines, a privately-owned, international real estate firm, serves as the property manager redeveloper for 10100 Santa Monica Blvd. Hines managed building renovations that took place in 1999, which included the lobby, exterior plazas and other common areas, along with upgrading operational systems and providing updated, on-site amenities.
The Challenge
Years of acid rain, pollutants, sun exposure and other extreme weather conditions caused the finish on the anodized aluminum panels of the building to fail. The building was last coated in the 1990s, but that most recent coating had also been adversely affected by the elements. Stuart Dean’s challenge was to restore the anodized aluminum panels to their original luster by applying an aluminum preservative. Stuart Dean associates faced a number of challenges based on the timing of the project, (December through April). They had to plan for the increased possibility of rain and high winds, which prompted the need for swing stage set-up and additional safety precautions.
The Solution
Stuart Dean designed a customized applicator that could deliver the aluminum preservative to five-foot-high aluminum panels in one application. The building was stripped and cleaned in the evenings to ensure the building’s day-to-day operations and activities were not affected by the restoration work. Additionally, the aluminum preservative was applied on Saturdays to reduce the smell for tenants during the week. Stuart Dean also performed interior stainless steel restoration and stone maintenance. Stuart Dean also restored 25 teak wood benches in the exterior plaza.
The Benefits
Stuart Dean estimated the job would take four to six months because of the winter and rain season but completed the job in approximately five months. Day-to-day operation and activities in the building were not affected during the restoration. The dramatic difference in the anodized aluminum from “before to after” gave the building a true facelift, completely restoring the surface to its original condition.